中国石油网消息(记者 李芳 通讯员 李政峰)记者从广西石化7月14日召开的月度经济活动分析会上获悉,今年上半年,广西石化生产运行进一步优化,完全加工费同比降低22.39元/吨,实现全厂降碳近3万吨,绿色发展成效进一步巩固拓展。
在“双碳”目标下,广西石化以“敢想敢干、善作善成”的“停锅炉”为引领,对蒸汽、氢气、氮气、水等系统实施低碳化改造,构建原油全流程优化、能量动态监控等数字化管理体系。这一系列举措使公司碳排放强度持续降低,自2020年起累计减排超100万吨,为炼化行业绿色转型提供可复制经验。
在蒸汽系统优化方面,广西石化通过蒸汽供给侧的原油重质化、降低催化原料残炭率、提升生焦炭率,优化350万吨/年催化裂化装置“两器”操作等举措增加蒸汽产出。在蒸汽消耗侧,广西石化提高新氢管网纯度削减蒸汽消耗,优化催化裂化装置气压机组运行等。通过这些努力,2019年4月,广西石化停止外购蒸汽,2020年7月3台锅炉全部停运,成为国内首个停运动力锅炉的炼厂。
动力锅炉停运后,广西石化积极优化蒸汽系统应急预案,总结出蒸汽系统运行“五大应急”工况,明确暴雨各阶段装置调整要点,全厂富余50吨/小时应急调峰蒸汽。在管网系统优化方面,公司以实现蒸汽管网减温减压器“零流量”为目标,开发能效管控分析平台,使低压蒸汽管网由“紧缺型”转为“过剩型”,动力锅炉实现了常态化停运。
此外,广西石化开展氢气、氮气和水等全系统优化。其中,2018年起,公司实施“合同能源管理”模式,启动氢气回收项目,实现氢气梯级提浓,吨油氢气消耗降幅达25%。公司优化氮气系统,空分空压装置实现单系列长周期运行,每小时用氮量下降40%,每天可节电5万千瓦时。公司通过水系统深度治理,每年雨水回用量达百万吨,污水回用率提高了13.7个百分点。
通过一系列系统性优化,广西石化员工观念转变,创新优化意识不断强化,构建了原油“全流程优化体系”、多系统“实时动态监控和能量移动追踪体系”、公用工程系统“数字化管控体系”、全厂蒸汽系统“应急体系”等,推动生产管理数字化转型。收获管理效益的同时,生态效益显著,全厂碳排放强度降幅达27.5%,累计碳减排超100万吨,树立绿色发展标杆。








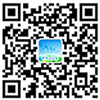